Biosolids Management
Biosolids are a nutrient-rich and organic byproduct of the wastewater treatment process. They are a result of the treatment of sewage in a wastewater treatment plant. When treated and processed, biosolids can be recycled and used as fertilizer to maintain or improve soil conditions and promote plant growth. In 2005, the City of Hamilton undertook a Biosolids Master Plan to address the challenges associated with the existing practice of biosolid management at the Woodward Wastewater Treatment Plant.
How are they treated in Hamilton?
Previously, biosolids from Hamilton were dewatered at the plant as a Class B material and re-used as a land-applied source of nutrient via the City’s land application contractor. Seasonal and climatic limitations, however, meant that a percentage of the biosolids were sent to landfill as ‘non-beneficial’ end use due to the loss of offsite storage.
While both Class A & B biosolids contain important nutrients and organic matter, in Class A biosolids, pathogens must be reduced to virtually non-detectable levels and the material must also comply with strict standards regarding metals and odours. Class B biosolids are treated but contain higher levels of detectable pathogens than Class A biosolids and may require a permit from the EPA with conditions on land application, crop harvesting and public access. With advances in technology, such as the new technology being used in Hamilton, many organizations are shifting away from Class B biosolids and investing in Class A biosolids.
Work began on a new Biosolids Management Process in June 2017 and began operations in May 2020.
The new management process takes up to 60,000 wet tones of wastewater biosolids and dries it into a food grade pellet or Product regulated under the Canadian Food Inspection Agency. The Biosolids Management Project was created to develop a long-term sustainable solution for the City’s biosolids, moving away from a wet sludge Class B material to a Class A product through a pelletization process. The end product can now be sold and used as fertilizer or used as fuel replacement.
Dewatered biosolids are pumped to storage via the existing dewatered sludge-pumping system. It is then pumped from either of the two biosolid storage silos into the mixer and mixed with recycled dry product to create a pellet for drying. The pellets are dropped into the inlet of the drum dryer, between the furnace and the drum. Recirculated gas and combustion air are mixed and heated in the furnace using natural gas. The evaporation of water from the preformed pellets takes place in the rotating drum. High-speed gas, along with drum rotation, conveys the pellets through the drum until they are dry enough, and thus light enough, to be conveyed out of the drum. At the exit of the drum, the process air carries evaporated moisture and dried particles via a ceramic-lined duct to the two stage separation system, which consists of a pre-separator and a polyclone, where the solids are separated from the process air stream.
The dried material exiting the equipment that separates the process air from the solids consists of dry particles of many sizes that drop onto a screen and are then classified by size. Trash is screened first, and this drops to a trash bin. Coarse and oversize pellets are dropped into a roll crusher and sent to the recycle bin along with the fine particles. The remaining material (approximately 0.5 mm to 4 mm in size) is conveyed to a pellet cooler and then pneumatically conveyed to pellet storage. The product is loaded into trucks via a screw conveyor with three dustless load-out chutes. The load-out system is designed such that pellet oil may be added to minimize dust generation during transport and use.
The hot process air exiting the separation equipment carries the evaporated water vapour and some very fine particulate. An impingement tray condenser/sub-cooler cools the process air, causing the evaporated moisture to condense and drop out while at the same time removing the particulates and condensable volatile organic compounds (VOCs). Most of the process air is recirculated back to the furnace and remains in the process loop, thus minimizing air emissions. The remainder passes through a Venturi scrubber and a three-chamber regenerative thermal oxidizer (‘RTO’) before exiting the system and entering the atmosphere through a stack.
The drying system incorporates process dust–collection systems using fabric filters to remove dust from a number of enclosed sources, including the conveyors, screen, pellet cooler, product silo, and load-out chutes. The collected dust is recycled into the process or removed as trash. The dust collectors are ducted to the odour-control system for treatment. Dryer process safety systems include emergency quench, spark quench, carbon monoxide and oxygen monitoring, temperature monitoring, and other safety mechanisms as required by NFPA 68, 69, and 820. There is also a nitrogen-blanketing system for the product silo and recycle bin.
The dryer utilizes mineral oil or a similar non-hazardous product as a dust suppressant for the beneficial product. The oil is stored in a double-walled tank with secondary containment. The required utilities include electricity, natural gas, effluent water, and potable water. Process wastewater discharges will be from the tray and Venturi scrubbers.
The project allows the City for the processing and marketing of biosolids in the most efficient manner, providing fixed known cost over a 30-year period that was validated through a predetermined affordability threshold. The public-private-partnership was supported through funding from Infrastructure Canada under the P3 Canada Fund, and the construction and continued operation and maintenance of the new facility will be led by Harbour City Solutions.
Immediate Benefits
- Minimal dust
- Lower odour
- Greater marketable opportunities as a pathogen-free pellet product
- Less truck traffic (from 20/week to 6/week)
- Less waste to landfills
- Greater cost certainty over the 30-year term
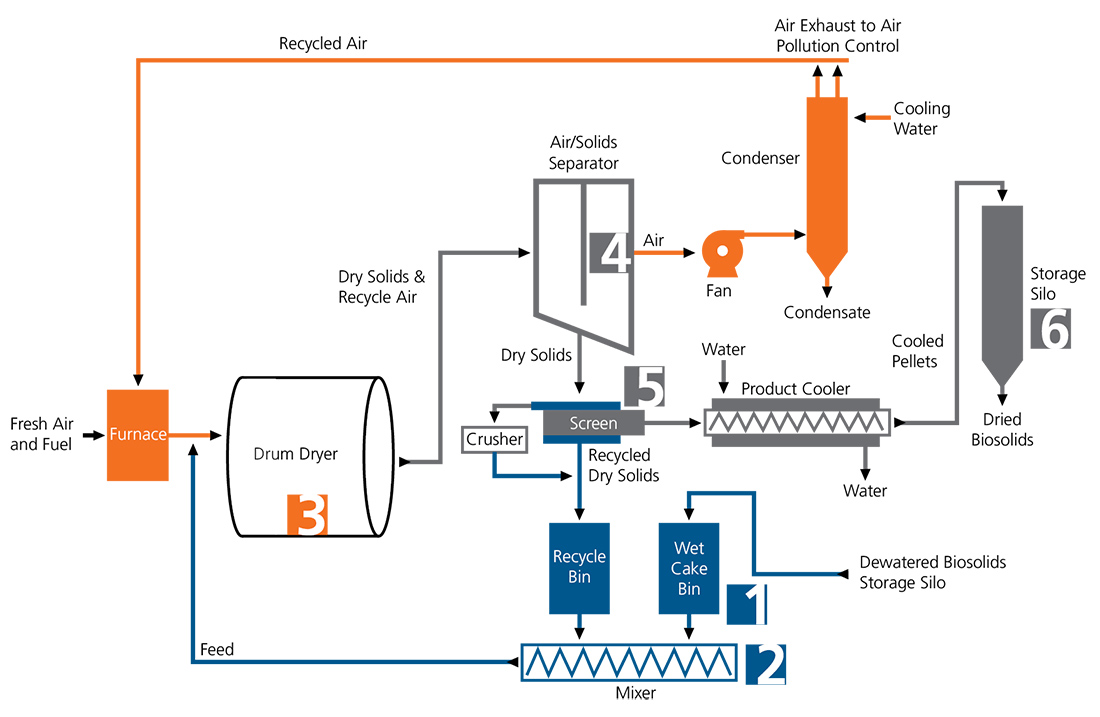
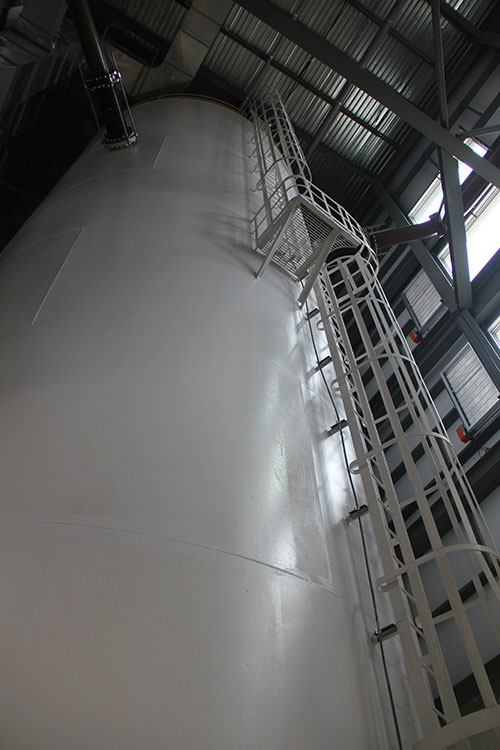
Dewatered Biosolids Storage Silos
Dewatered biosolids are pumped to storage via the existing dewatered sludge-pumping system.
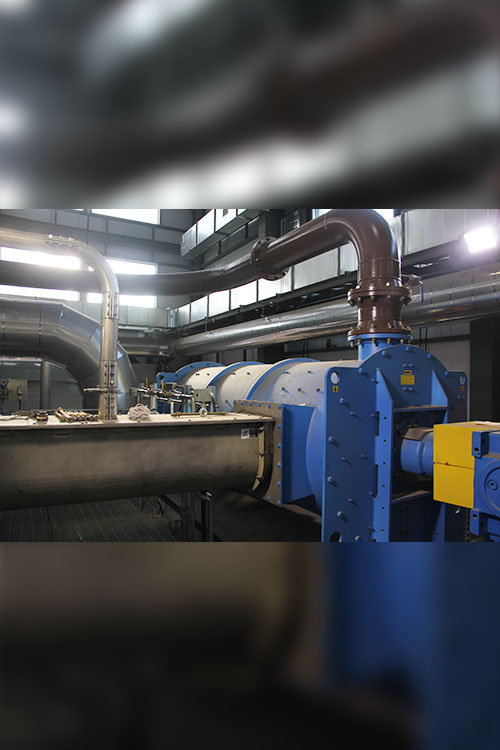
Mixer
Dewatered biosolids are pumped from storage silos into the mixer to be mixed with recycled dry product; this creates a suitable pellet for drying.
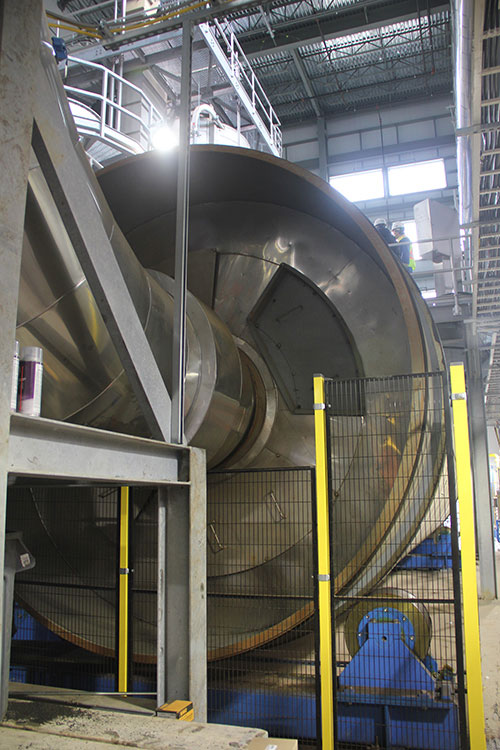
Drum Dryer
Pellets are dropped into the inlet of the drum dryer, between the furnace and the drum. Recirculated gas and combustion air are mixed and heated in the furnace using natural gas and remove water from the preformed pellets.
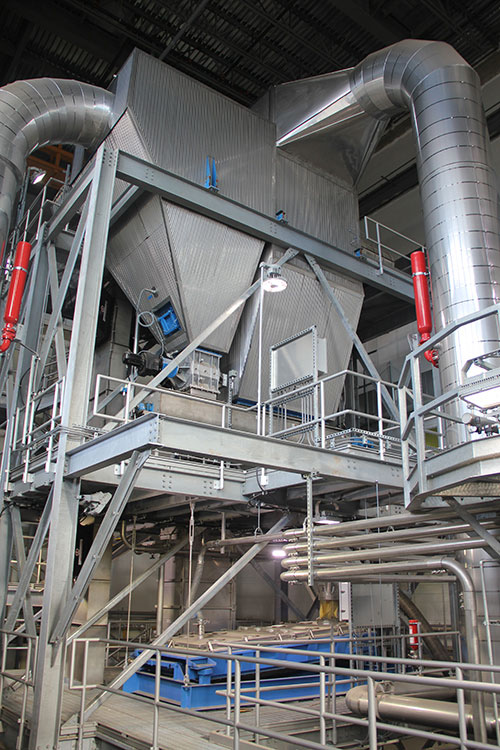
Air/Solids Separator
Once they exit the drum, the evaporated moisture and dried particles are carried to a two-stage separation system. This allows the solids to be separated from the process air stream.
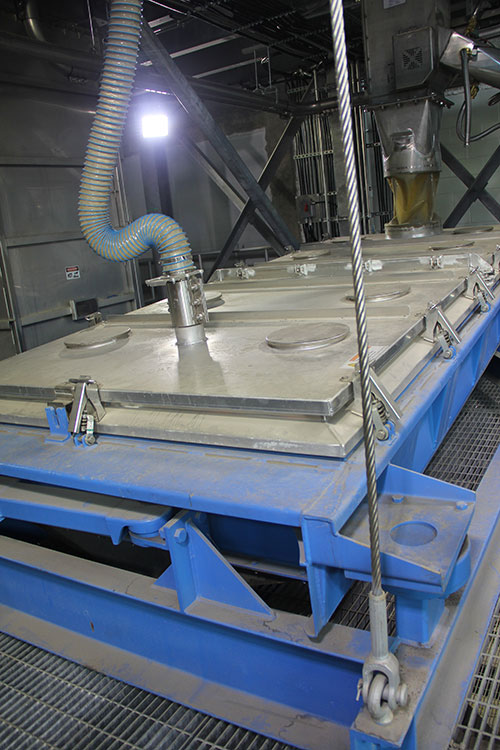
Shaker Screen
This process sorts the dried pellets by size. Trash is screened first and drops to a trash bin. Coarse and oversize pellets are dropped into a roll crusher and sent to the recycle bin along with the fine particles. The remaining material (approximately 0.5 mm to 4 mm in size) is conveyed to a pellet cooler and then pneumatically conveyed to pellet storage.
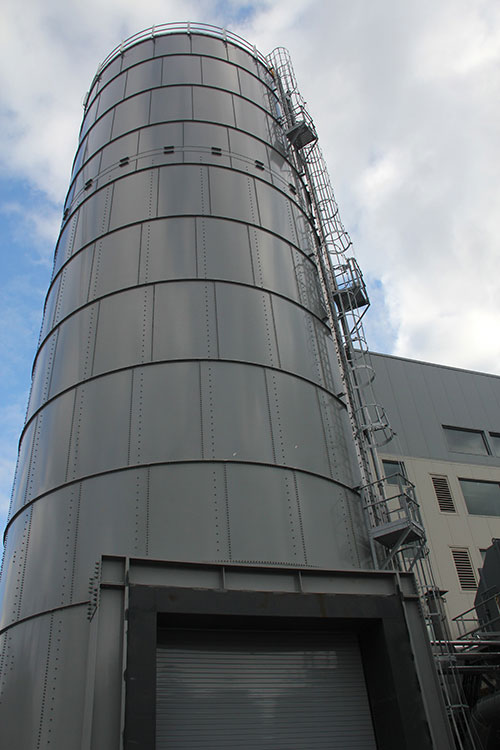
Storage Silo
This is where screened and cooled pellets that are not recycled are stored. The product is loaded into trucks via a screw conveyor with three dustless load-out chutes and is sold for fertilizer or fuel.